Best Practices for Preventing Weld Undercut: Grasping the Basics
Wiki Article
Mastering the Art of Welding: How to Avoid Undercut Welding Issues for Flawless Construction Results
By understanding the root creates of undercut welding and executing efficient techniques to stop it, welders can boost their craft to new degrees of quality. In the quest of remarkable construction outcomes, grasping the art of welding to avoid undercut issues is not simply an ability yet a requirement for those aiming for perfection in their work.Comprehending Undercut Welding

To stop undercut welding, welders should ensure proper welding criteria, such as adjusting the present, voltage, traveling rate, and preserving the right electrode angle. By understanding the reasons of undercut welding and carrying out preventative procedures, welders can achieve high-quality, structurally sound welds.
Reasons of Undercut in Welding
Comprehending the elements that add to undercut in welding is essential for welders to create premium, structurally audio welds. Poor welding incorrect or present welding rate can likewise contribute to damage. Understanding these reasons and implementing correct welding techniques can help stop undercutting issues, ensuring strong and durable welds.Methods to Prevent Undercutting

To reduce the risk of damaging in welding, welders can employ tactical welding techniques intended at boosting the quality and stability of the weld joints. Furthermore, making use of the correct welding technique for the particular joint configuration, such as weave or stringer grains, can add to minimizing damaging.
Employing back-step welding strategies and regulating the weld grain account can additionally assist disperse heat equally and minimize the danger of undercut. Normal assessment of the weld joint during and after welding, as well pop over to this site as carrying out top quality assurance procedures, can assist in finding and dealing with undercutting problems immediately.
Relevance of Appropriate Welding Criteria
Choosing and keeping appropriate welding visit site parameters is necessary for achieving effective welds with very little flaws. Welding specifications describe variables such as voltage, current, travel speed, electrode angle, and shielding gas flow rate that straight affect the welding process. These parameters need to be thoroughly adjusted based upon the kind of material being welded, its density, and the welding strategy utilized.Proper welding criteria make sure the correct amount of heat is put on melt the base metals and filler product evenly. If the parameters are established expensive, it can bring about extreme warm input, causing burn-through, spatter, or distortion. On the various other hand, if the criteria are too low, insufficient combination, lack of infiltration, or undercutting may occur.
Quality Assurance in Welding Procedures
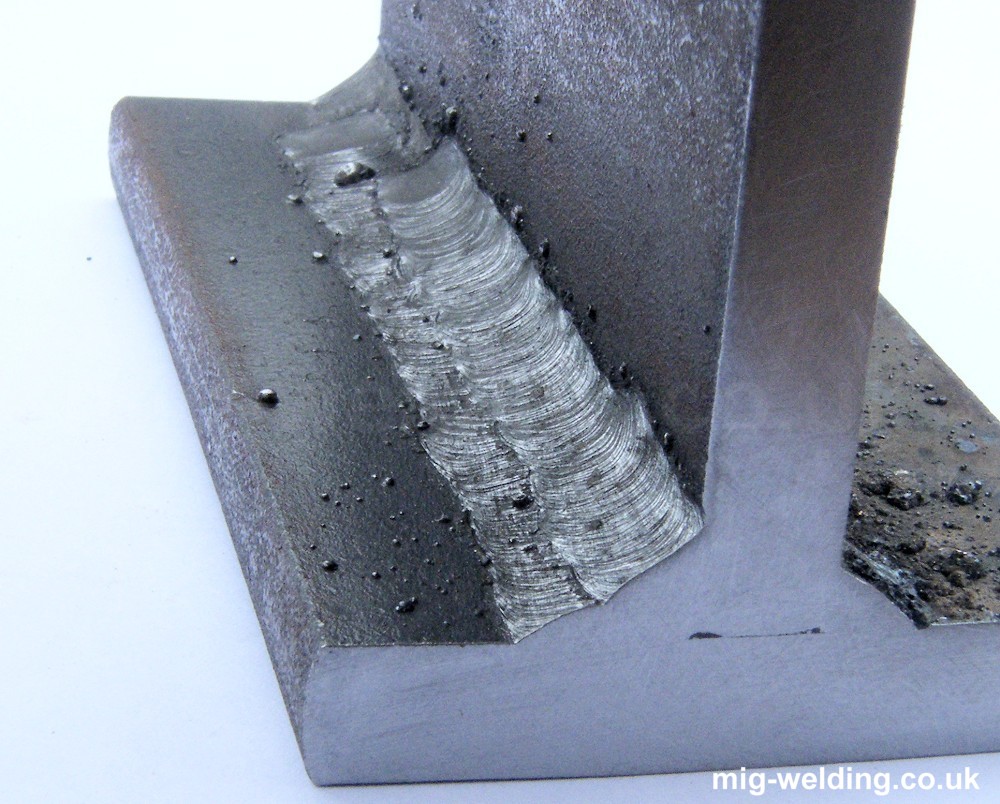
Verdict
To conclude, grasping the art of welding requires a complete understanding of undercut welding, its causes, and strategies to stop it. By making certain correct welding criteria and implementing quality control techniques, remarkable fabrication outcomes can be attained. It is important for welders to regularly strive for excellence in their welding procedures to prevent undercut problems and create top quality welds.Undercut welding, a typical defect in welding processes, takes place when the weld metal doesn't effectively fill the groove and leaves a groove or anxiety along the bonded joint.To avoid undercut welding, welders ought to ensure correct welding criteria, such as adjusting the current, voltage, traveling speed, and maintaining the proper electrode angle. Poor welding incorrect or current welding rate can likewise contribute to undercut.To mitigate the danger of undercutting in welding, welders can utilize tactical welding techniques aimed at boosting the high quality and honesty of the weld joints.In conclusion, grasping the art of welding requires a comprehensive understanding of undercut welding, its causes, and techniques to stop it.
Report this wiki page